How Are Headphones Made?
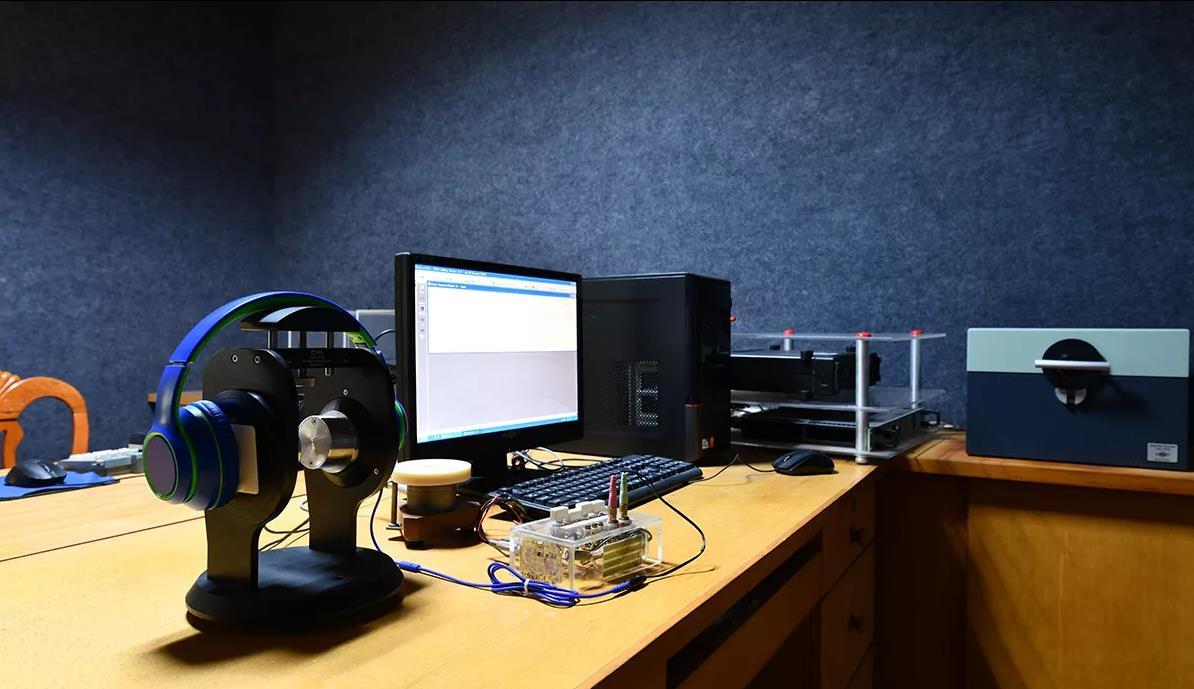
Have you ever wondered how headphones are made? Due to their high demand, we seem to know a lot about headphones. People from all walks of life use headphones—whether athletes, gamers, music lovers, or for the simple pleasure of listening to music every day.
They're easy to set up, and with innovative technology, we've learned how to optimize their power. When it comes to care and maintenance, we've also come up with clever ways to extend life. Headphones have become an extension of ourselves due to their utility and entertainment value.
But did you know that headphones are made? In this article, you will learn how to make headphones.
Materials used in the production of headphones
Headphones are made up of smaller components that work together to allow us to listen to music, news, and anything audible in private.
Below are the basic materials used to produce headphones. These are basically the same materials that were used in the first earphones.
The latest headphone models add more advanced versions of the same materials, with the latest technologies that enhance our listening experience.
The following are the basic materials used to produce headphones:
PVC
Plastic
Rubber
Faux leather
Memory foam
Copper
Ceramics
Other metals
The most common design we see today is the "on-ear" configuration. This design features the speaker held in place by a piece of plastic wrapped in foam and leather. This headset is designed to curve around the head for optimal functionality and aesthetics.
What are the basic components of headphones?
Here are the most important components inside the headset:
Case
The front and rear of the headphone unit subtly cover all the components, which in turn helps in safe and efficient access to or above our ears. They usually have cushions that reduce the risk of ear swelling or pain.
Rubber sealed loop
This assembly holds the case together and ensures that the earphones themselves don't come apart.
Electric wire
These components transmit audio signals. In the case of wireless headphones, Bluetooth technology is used to transmit the signal.
Magnet
This can be found on the rear of the speaker. A large part of the weight of the earphones is due to the magnets installed inside the earphones.
Copper coil
It acts as an electromagnet whenever an electric current passes through it. It's the same type of coil used in guitar pickups.
Diaphragm
It's a plastic cone that makes a sound when it vibrates.
All these components are very sensitive. Therefore, it is always advisable to handle it with extreme care. Top-notch headphones are often handcrafted by dedicated professionals and technicians.
How are headphones made?
So how do all these materials and components come together to make a headset? Here's how the production process works:
Once the design is complete, the molding machine shapes the plastic parts.
The winding machine winds the copper wire around the cylinder. The standard number of copper coils is 10,000 turns, but in general, the more coils, the better the electromagnetic performance.
The resulting copper coil now becomes a voice coil, which is then sealed by a technician with a clear diaphragm or plastic cover. For sealing, use a small amount of glue and a UV light for the best results.
The voice coil is then installed into the housing, which is carefully positioned to produce the best possible sound.
Micro speakers go through a series of frequency range and distortion tests before final assembly.
Finished installing wires in the adjustable strap strain relief. The logo of the headphones and other relevant details are printed on the finished product.
The above briefly introduces some manufacturing processes of earphones. If you want to customize or buy earphones, please contact us.
JunYe is a professional custom earphone manufacturer. JunYe manufactures almost all parts of wired earbuds and wired headphones, such as earmuffs, headbands, cables, speakers, etc. We have grinding machines, wire extrusion lines, injection molding machines, charging cabinets, etc. We can complete bare metal tests and package tests according to customers' requirements, such as headband tensile test, drop test, low temperature/high-temperature tests, and fogging tests.